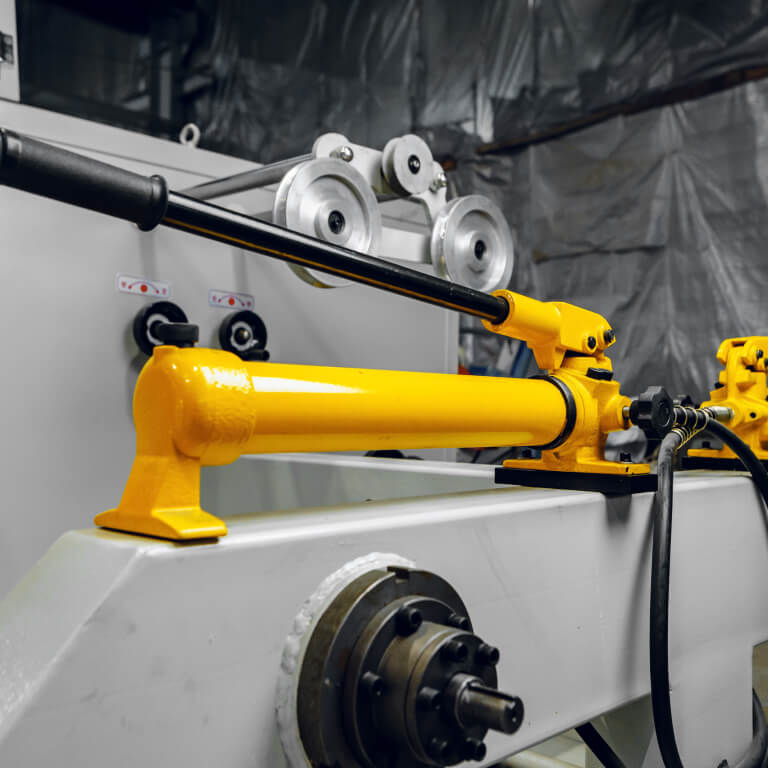
Concrete Roof Tile Machines
Machines – up to 130 tpm
- Mixing plant – batch and continuous
- Extruder drive units and making heads
- Guillotine units
- Colour applicators
- Rotary drying units
- Racking – fully automatic
- Curing chambers – stationary and conveyor systems
- Depalletors
- Sealant Applicators
- Conveying
- Recycling systems
Installations
Spare Parts
Service
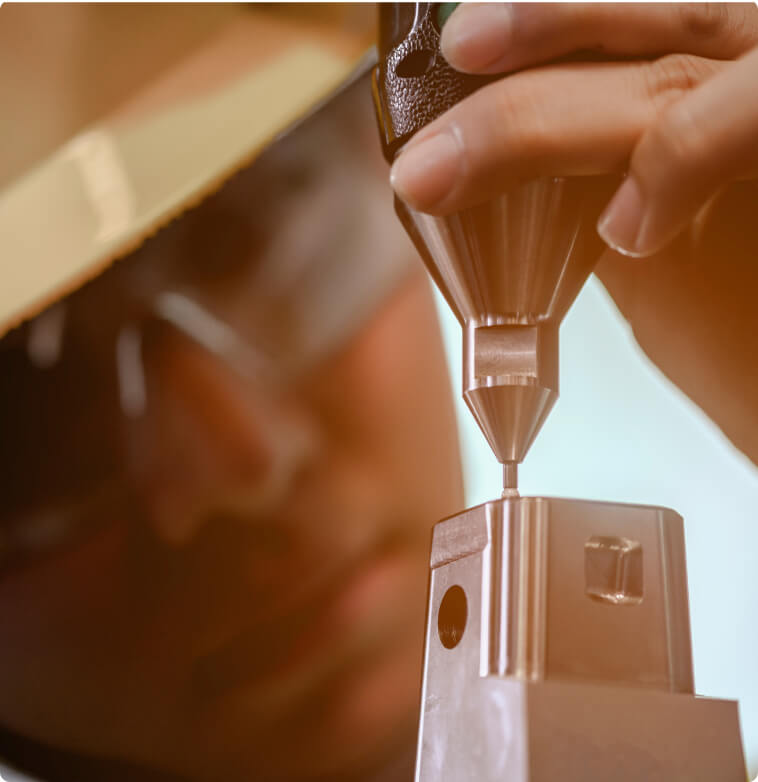
Engineering Solutions
Arrow MPS has many years of experience in manufacturing and process engineering. We can design, test, develop and install an entire solution for any manufacturing or industrial problem. From a simple timber pallet alignment tool or machinery enclosures up to complex automotive test cells or precious metal reclamation plants our experience and capabilities make us a valuable partner.
If you have a problem that needs to be solved, please get in touch – we will be happy to spend some time discussing your requirements and volunteering some ideas on how it may be solved. This is our passion and the reason are in business.
Precision Machining – Milling, Turning and Grinding.
The genesis of Arrow MPS was Turmac Engineering, first established in 1964. Our original expertise in precision engineering remains today, although our tools have been thoroughly modernised. We maintain a mix of computer numerical control lathes and mills along with a wide range of specialised manual machines that allow us to produce the most complex parts and assemblies.
We are equally at home working to supplied drawings or to samples provided by you. However our service doesn’t stop there. We can design parts to upgrade your current machinery, undertake the necessary analysis to ensure they will integrate with your plant, produce drawings and supply parts. If required we are also happy to hold stock for you to ensure you are never caught short.
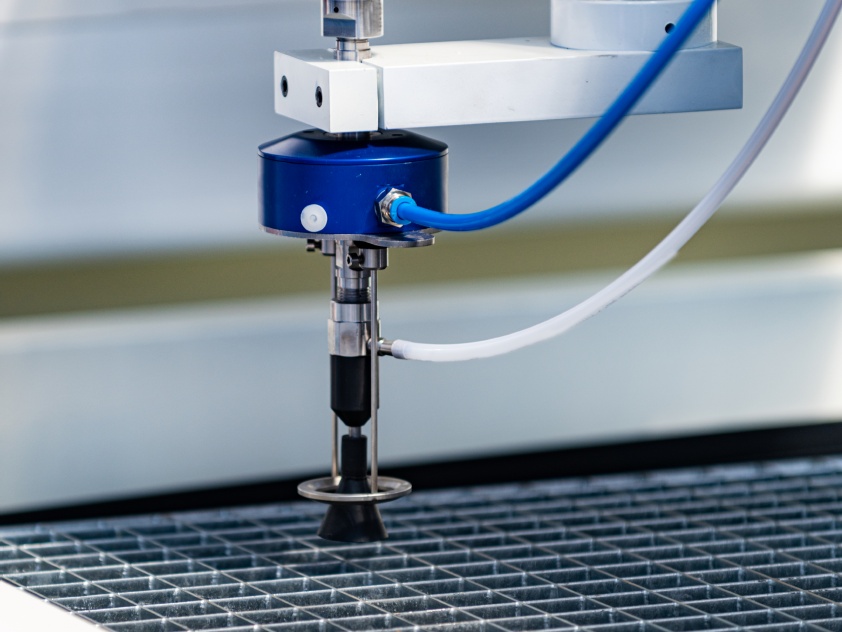
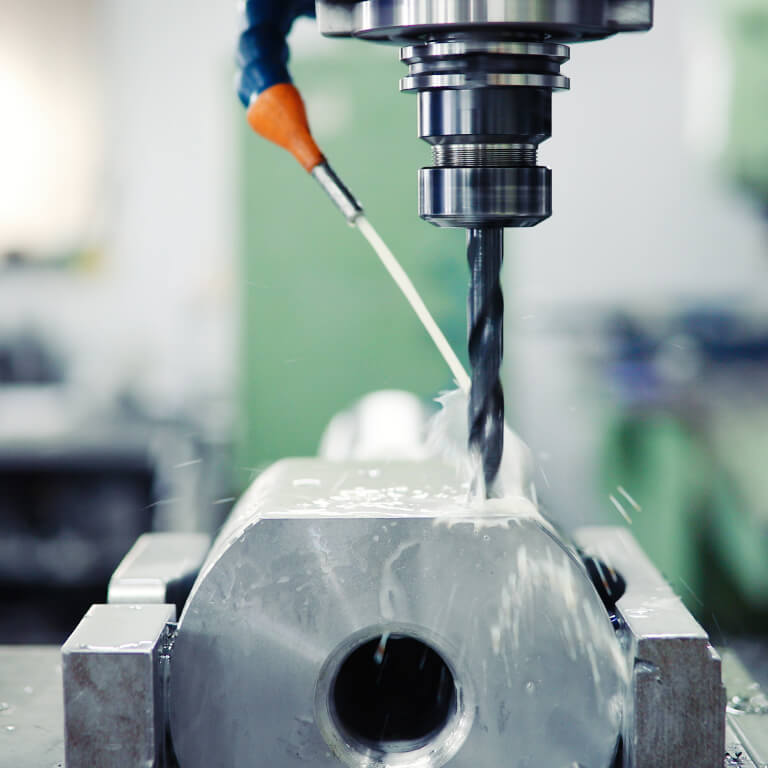
Tungsten Carbide
For high wear applications you cannot go past Tungsten Carbide. With a density more than twice that of steel Tungsten Carbide can give years of service where a hardened steel of up to 62 Rockwell will last only a few months.
Our considerable experience with Tungsten Carbide comes from years of working with the extrusion of concrete in the roof tile industry. We can specify material grade, optimum shape and application for your particular needs.
Some applications of tungsten carbide are
- Cutting tips for machining
- Forming rollers for abrasive materials
- Separating blades
- Bed plates for sliding contact
- Localised coating of high pressure or impact areas.
Tungsten carbide can be made as a solid component in intricate shapes, applied as a coating for thicknesses up to 1 mm or combined with steel backing plates to form composites. In most high wear circumstances Tungsten Carbide is the economically responsible choice.